How we make glass?
Guangdong Shengwei Glass Technology Co., Ltd.
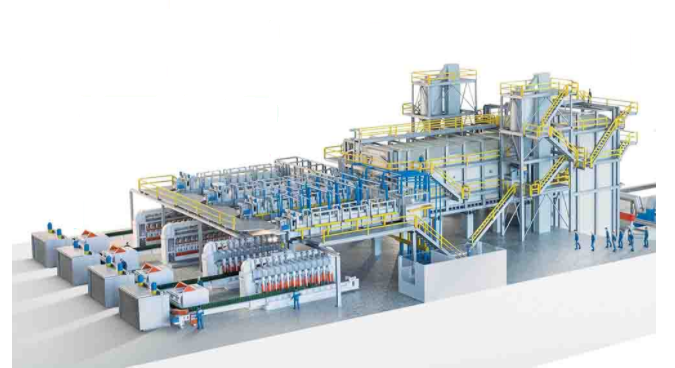
Shengwei has two electric furnace with a daily output of 50 tons, with a furance area of 10*2 square meters The furnace adopts electric way to melt liquid glass, which has the advantages of no waste gas pollution, high thermal efficiency, easy handling and energy saving.

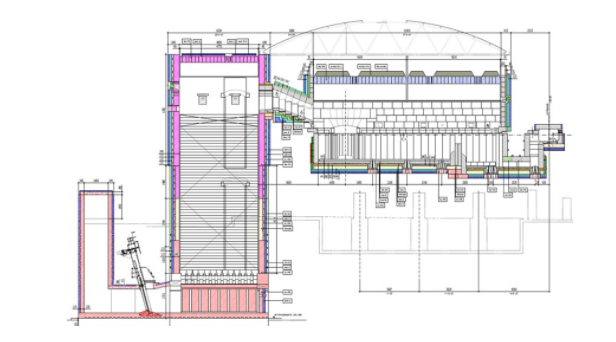
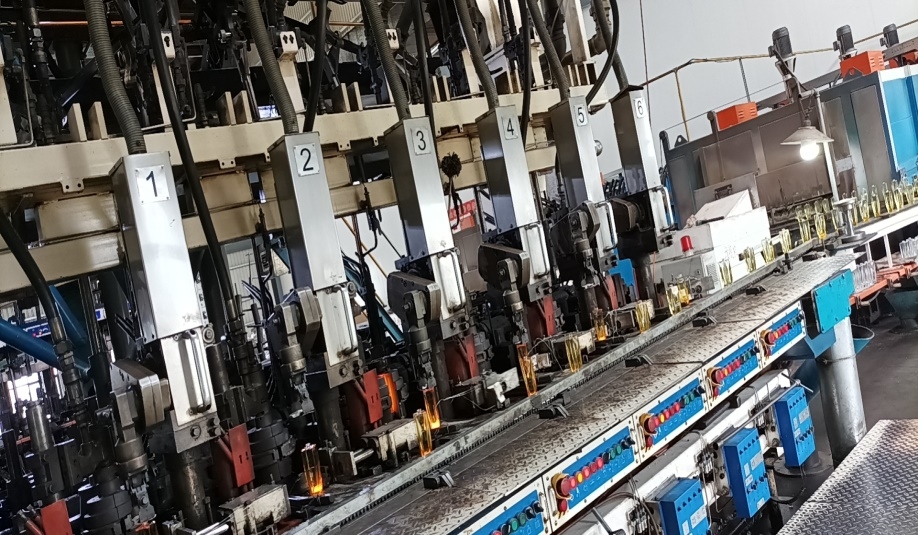
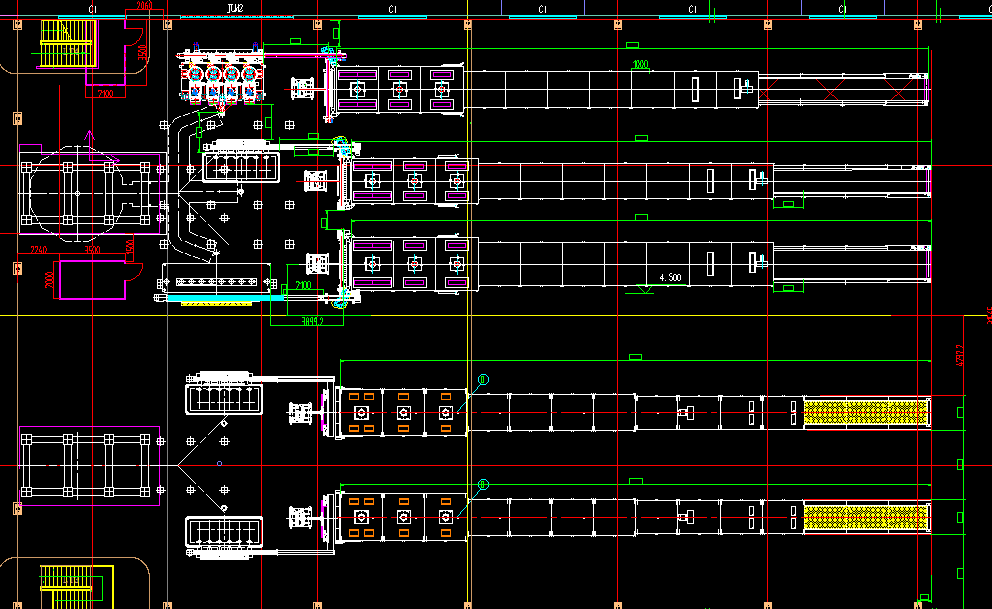
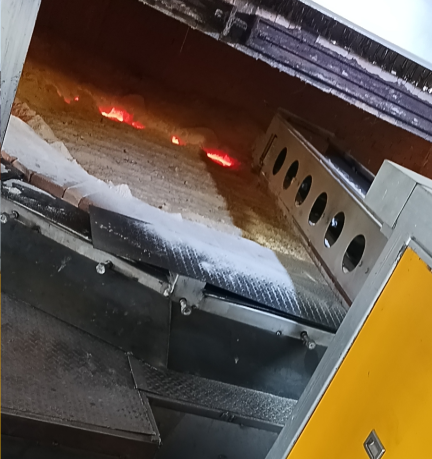
The production flow
1、Feeding and melting: Weighing and dosing——mixing——conveying——feeder——melting pool 1500 degrees——working pool2、Feeding: feeding channel —— feeding basin —— mud bowl —— cutting —— dropping 1100 degrees —— feeding pipe3. Production moulding: row and column machine —— initial mold —— turnover —— molding —— molding 550 degrees —— bottle clamping – bottle pulling —— turning machine4. Annealing: machine push the bottle into annealing furnace —— annealing furnace heating 550-580 degrees —— holding for 20 minutes —— slow cooling process (slow cooling to 430 degrees) —— quick cooling out (annealing time is generally about 1.5 hours)5. Inspection: 100% full inspection by light on —— packaging —— sampling inspection by QC —— put into the warehouse
The No.1 electric furnace production line can only produce products with the same weight. When changing the weight, it need to replace the mud bowl before making the next batch of products.When each time the mud bowl is replaced, there will be defects such as bubbles and dirty materials.
It will take about 2 hours for the liquid glass to return to normal.Therefore, the production plan is to arrange the products close to the weight section together, At the same time, the production line should also adjust the furnace discharge according to different weights to ensure that the overall furnace discharge is controlled within 1 ton.
Now the multi-weight feeding machines have been introduced to no.2 furnace. A single production line can produce products with different weights of about 10 to 15 grams at the same time, which is great help to reduce the frequency of changing production and increase the flexibility of products.
Shengwei is the second one use electric melting furnace in China for the production of cosmetic glass bottles.Under this guidance, the use of electric melting furnaces in the cosmetic glass bottle manufacturing industry is increasing.Hangzhou Samsung has also put into operation a 40 ton electric melting furnace, Nantong Xianglong, Pingxiang Gaocheng, Shanxi Xinda and other electric melting furnaces are in production, and Anhui Yijing plans to build an electric furnace.
There are also different configurations of production lines in the industry. Shengwei currently focuses on single drop models, which has great advantages in stable product production, stable functional & size and well control bottle body Hafts line.
There are two drop machines and three drop machines in the industry, which has a certain output value effect on the production of light weight bottles (35-100g) and products with large single quantity.Thanks for your attention.